熱點資訊
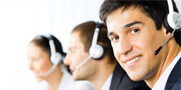
咨詢熱線:
028-83920379
郵件: 50402751@qq.com
電話:028-83920379
地址: 四川省成都市新都區(qū)工業(yè)東區(qū)永達(dá)路1151號
反應(yīng)釜提升產(chǎn)量的多維技術(shù)路徑與實踐應(yīng)用
在化工、制藥、材料等流程工業(yè)中,反應(yīng)釜作為核心生產(chǎn)設(shè)備,其運行效率直接決定著生產(chǎn)線的產(chǎn)能上限。通過技術(shù)升級、工藝優(yōu)化與智能管理的協(xié)同創(chuàng)新,反應(yīng)釜能夠在保證產(chǎn)品質(zhì)量的前提下實現(xiàn)產(chǎn)量的顯著提升。這種提升并非單一環(huán)節(jié)的改進(jìn),而是涵蓋設(shè)備性能增強(qiáng)、反應(yīng)條件精準(zhǔn)控制、能源利用效率提升等多維度的系統(tǒng)工程。
設(shè)備性能升級:突破物理限制的產(chǎn)能釋放
反應(yīng)釜的結(jié)構(gòu)設(shè)計革新是提升產(chǎn)量的基礎(chǔ)。傳統(tǒng)反應(yīng)釜受限于攪拌效率不足,往往存在物料混合不均、局部反應(yīng)不完全的問題,導(dǎo)致有效反應(yīng)時間延長。采用新型攪拌系統(tǒng)可有效解決這一痛點:錨式攪拌器配合側(cè)入式分散盤的組合設(shè)計,能使高黏度物料的混合效率提升 40% 以上;而對于固液兩相反應(yīng)體系,傾斜式槳葉搭配底部導(dǎo)流筒的結(jié)構(gòu),可將固體顆粒懸浮率從 60% 提高至 95%,大幅減少反應(yīng)死角。某精細(xì)化工企業(yè)通過將傳統(tǒng)平直槳更換為螺帶式攪拌器,使染料中間體的批次反應(yīng)時間從 8 小時縮短至 5 小時,單日產(chǎn)能提升 37.5%。
材質(zhì)升級同樣為產(chǎn)能提升提供支撐。鈦合金復(fù)合釜體相比傳統(tǒng)不銹鋼釜體,不僅耐腐蝕性提升 3 倍,其導(dǎo)熱系數(shù)提高 25%,使得升溫速率從每小時 15℃提升至 22℃,在需要嚴(yán)格控溫的聚合反應(yīng)中,單釜批次間隔縮短近 1 小時。而采用 316L 不銹鋼與哈氏合金的襯里技術(shù),可使反應(yīng)釜耐受更寬范圍的介質(zhì)濃度,實現(xiàn)從間歇式生產(chǎn)到連續(xù)化生產(chǎn)的轉(zhuǎn)變,某農(nóng)藥廠通過該技術(shù)改造,將草甘膦生產(chǎn)線的連續(xù)運行周期從 15 天延長至 30 天,年產(chǎn)能增加 1200 噸。
工藝參數(shù)優(yōu)化:精準(zhǔn)調(diào)控下的效率革命
反應(yīng)條件的精準(zhǔn)控制是提升反應(yīng)轉(zhuǎn)化率的關(guān)鍵。溫度波動每增加 ±2℃,某些精細(xì)化工產(chǎn)品的反應(yīng)收率可能下降 3%-5%。采用夾套與內(nèi)盤管組合溫控系統(tǒng),配合 PID 自適應(yīng)算法,可將釜內(nèi)溫度控制精度提升至 ±0.5℃,在己內(nèi)酰胺合成反應(yīng)中,使單程轉(zhuǎn)化率從 88% 提高至 92%。某化纖企業(yè)通過該技術(shù),在相同反應(yīng)時間內(nèi),每噸原料的產(chǎn)品產(chǎn)出增加 40 公斤。
壓力參數(shù)的優(yōu)化同樣創(chuàng)造顯著效益。在高壓加氫反應(yīng)中,采用梯度升壓工藝替代恒壓操作,可使催化劑活性保持時間延長 20%。某醫(yī)藥中間體生產(chǎn)企業(yè)通過建立壓力 - 時間曲線模型,將氫化反應(yīng)的催化劑更換周期從 15 批次延長至 18 批次,減少非生產(chǎn)時間 20 小時 / 月,年增產(chǎn)量約 30 噸。而對于氣相參與的反應(yīng),優(yōu)化進(jìn)氣分布器的孔徑與排布方式,可使氣體利用率提升 15%-20%,在甲醇合成反應(yīng)中實現(xiàn)單位體積產(chǎn)能提高 18%。
智能管理系統(tǒng):數(shù)據(jù)驅(qū)動的產(chǎn)能最大化
物聯(lián)網(wǎng)技術(shù)的應(yīng)用重構(gòu)了反應(yīng)釜的運行管理模式。通過在釜體、管道、電機(jī)等關(guān)鍵部位部署振動、溫度、壓力等傳感器陣列,可實時采集 100 余項運行參數(shù),建立反應(yīng)過程的數(shù)字孿生模型。某化工園區(qū)的智能監(jiān)控平臺通過分析歷史數(shù)據(jù)發(fā)現(xiàn),當(dāng)攪拌電機(jī)電流波動超過 5% 時,反應(yīng)轉(zhuǎn)化率會出現(xiàn)顯著下降,據(jù)此調(diào)整的動態(tài)負(fù)載平衡系統(tǒng),使單釜有效運行時間提升 6%。
預(yù)測性維護(hù)體系的建立大幅減少非計劃停機(jī)。傳統(tǒng)定期維護(hù)模式往往導(dǎo)致過度維修或故障突發(fā),某樹脂生產(chǎn)企業(yè)引入振動頻譜分析技術(shù)后,能提前 72 小時預(yù)測攪拌軸軸承的磨損趨勢,將非計劃停機(jī)時間從每年 45 小時降至 15 小時,直接增加產(chǎn)量約 800 噸。而基于機(jī)器學(xué)習(xí)的能耗優(yōu)化算法,可根據(jù)實時反應(yīng)進(jìn)度自動調(diào)節(jié)加熱功率,在丙烯酸酯生產(chǎn)中實現(xiàn)單位產(chǎn)品能耗下降 12%,間接提升設(shè)備有效運行時間。
連續(xù)化生產(chǎn)改造:從間歇到流程的產(chǎn)能飛躍
將間歇式反應(yīng)釜改造為連續(xù)流反應(yīng)系統(tǒng),是產(chǎn)能提升的革命性突破。采用多釜串聯(lián)耦合技術(shù),通過精確控制物料在各釜之間的停留時間,可使反應(yīng)效率提升 50% 以上。某染料廠將 3 臺 5000L 間歇釜改造為串聯(lián)連續(xù)反應(yīng)系統(tǒng),配合在線檢測與自動補(bǔ)料裝置,使日產(chǎn)量從 12 噸提升至 20 噸,同時減少人工操作強(qiáng)度 60%。
微通道反應(yīng)技術(shù)與傳統(tǒng)反應(yīng)釜的組合應(yīng)用,在危險反應(yīng)中展現(xiàn)獨特優(yōu)勢。在硝化反應(yīng)中,采用微通道反應(yīng)器進(jìn)行預(yù)混合與初步反應(yīng),再進(jìn)入反應(yīng)釜完成深度反應(yīng),可使反應(yīng)時間從 8 小時縮短至 3 小時,且放熱量降低 60%,實現(xiàn)產(chǎn)能翻倍的同時提升安全性。某含能材料企業(yè)通過該組合工藝,將梯恩梯生產(chǎn)的批次間隔從 12 小時壓縮至 5 小時,年產(chǎn)能提升 140%。
反應(yīng)釜產(chǎn)量的提升是設(shè)備性能、工藝水平與管理能力協(xié)同進(jìn)步的結(jié)果。從單釜效率優(yōu)化到系統(tǒng)集成創(chuàng)新,每一個技術(shù)突破都帶來產(chǎn)能的階梯式增長。隨著智能制造與綠色化工的深入發(fā)展,反應(yīng)釜將通過更精準(zhǔn)的控制、更高效的能源利用和更靈活的生產(chǎn)組織模式,持續(xù)釋放產(chǎn)能潛力,為流程工業(yè)的高質(zhì)量發(fā)展提供核心動力。